Sustainability
Advancing technologies and business solutions to drive a sustainable future
Strong environmental, social and governance performance is central to everything we do and everything we stand for. Our employees lead and innovate for the acceleration of a successful transition to a low-carbon future while providing the reliable energy and chemicals essential to society.
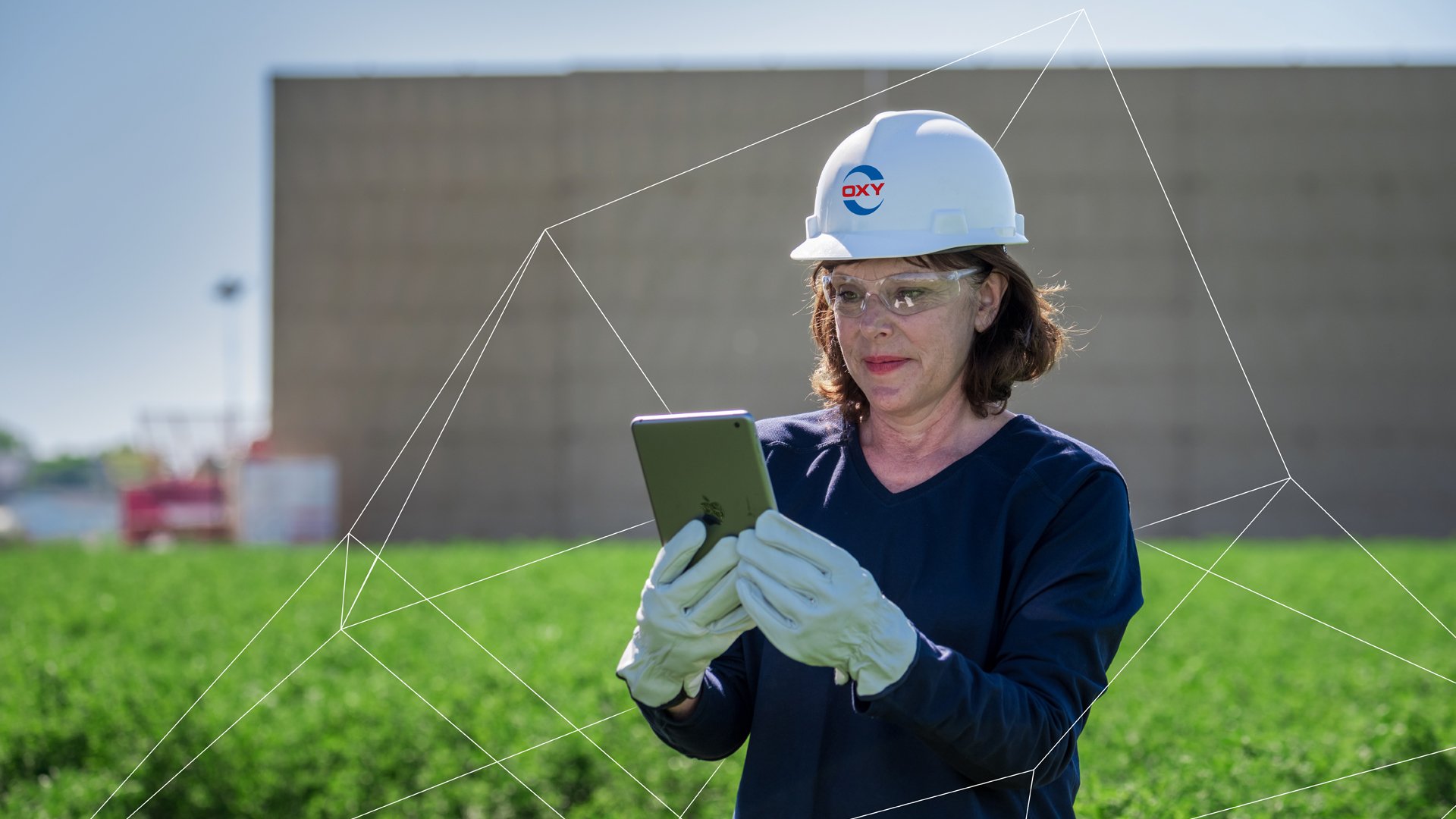
At Oxy, sustainability is fundamental to our success and reputation as the employer, neighbor and Partner of Choice®. We are dedicated to:
- Operating responsibly
- Protecting the environment and minimizing our footprint
- Upholding and promoting human rights
- Contributing to our neighboring communities and regional economies
- Providing safe, healthy and secure workplaces
- Maintaining high ethical standards
- Benefiting our stakeholders
- Respecting cultural norms and values everywhere we operate
We continually evaluate ways to integrate sustainability throughout our operations, improve our sustainability programs and performance, and transparently share our progress with stakeholders.
Four Pillars of Sustainability
Oxy was the first U.S. oil and gas company to endorse the World Economic Forum’s (WEF) Stakeholder Capitalism Metrics, a global framework that promotes transparency with investor and stakeholder engagement. Our sustainability reporting and strategy align with the WEF's four pillars of stakeholder capitalism: principles of governance, people, planet and prosperity. Each pillar represents a key focus area as Oxy continues to implement and enhance sustainable business practices and programs.
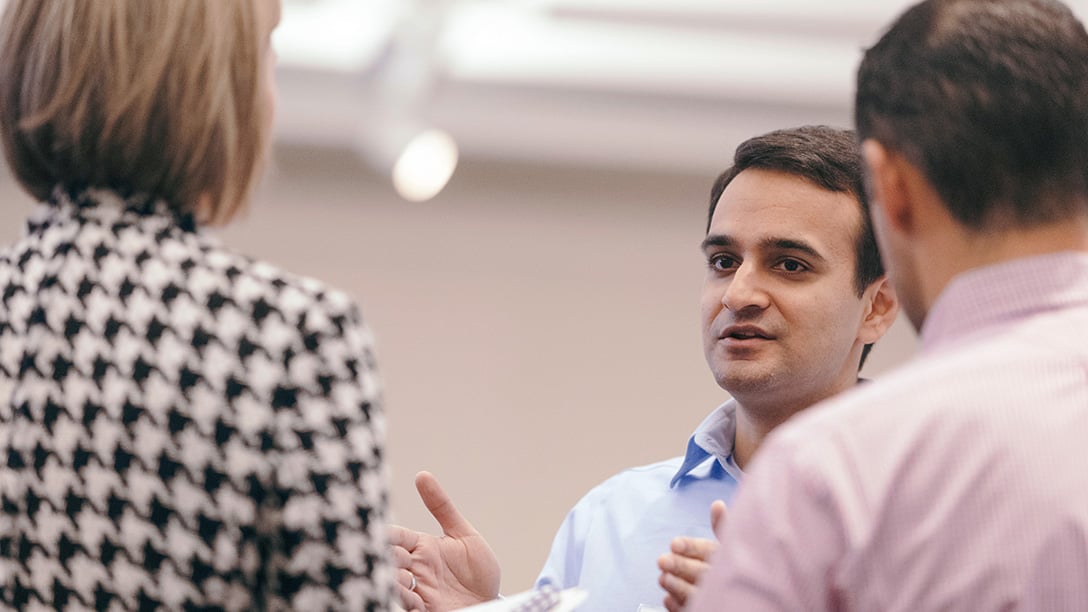
Principles of Governance
Our governance structure supports our drive to create value for our shareholders and benefit our communities and society as a sustainable leader in high-performance energy production, essential chemistry and carbon innovation. Our Board holds our leadership accountable with criteria that reflect Oxy’s mission, vision and values, our company's purpose and strategy, our commitment to ethical behavior in our Code of Business Conduct, and our attention to assessing risk and internal controls. We implement responsible policies and robust management systems to foster and reinforce business practices that are consistently sound, highly principled and transparent.
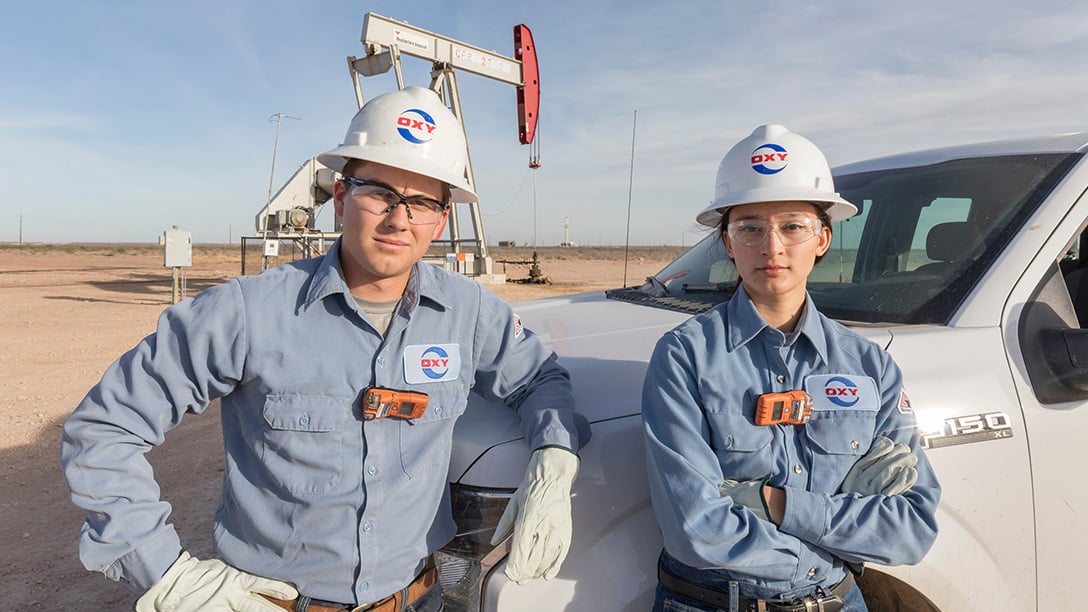
People
In our fast-paced, competitive industry, we strive to provide safe, supportive and high-quality work environments that reward innovation. Oxy’s human capital and workforce development strategy is rooted in Oxy’s core values, unequivocally empowered by the support of our leadership and executed in collaboration with business unit leaders across the organization. We believe our diverse global workforce creates value for our shareholders, business partners and host communities, provides a competitive advantage and delivers real progress toward Oxy’s mission and vision. Our exemplary safety performance reflects our commitment to protecting the health and safety of the people at our facilities and in the communities where we operate.
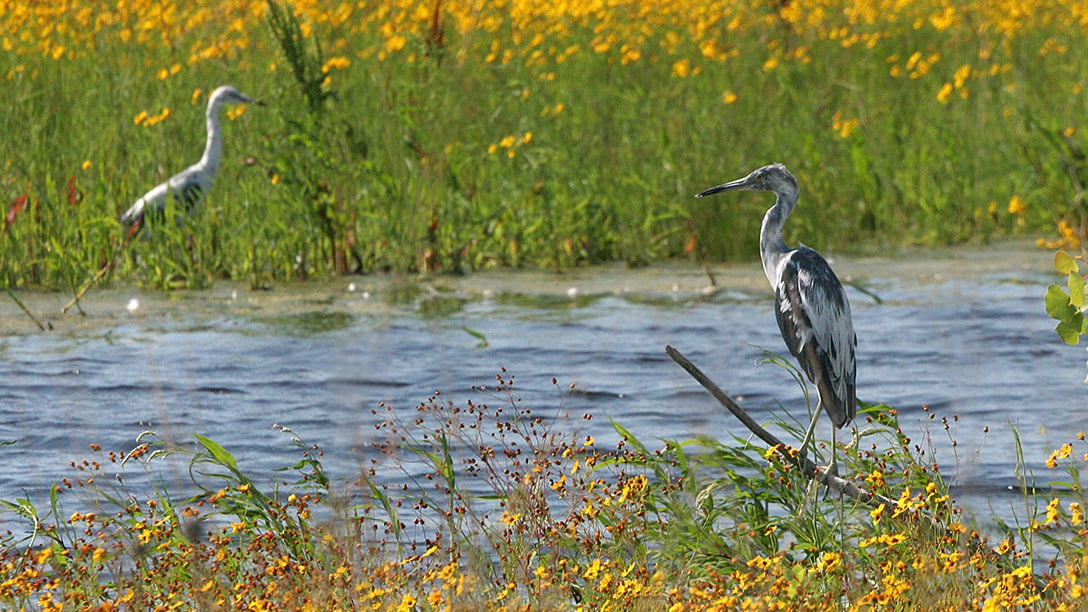
Planet
We integrate stewardship activities through rigorous policies and procedures that are designed to promote compliance with environmental laws, regulations and internal standards. Oxy applies innovative technologies to conserve and reuse resources, designs facilities to minimize our footprint near communities and ecosystems and works with stakeholders to preserve habitat and biodiversity. As a company with long-term investments in our properties, infrastructure and communities, sustaining environmental quality is central to the long-term prosperity of our businesses.
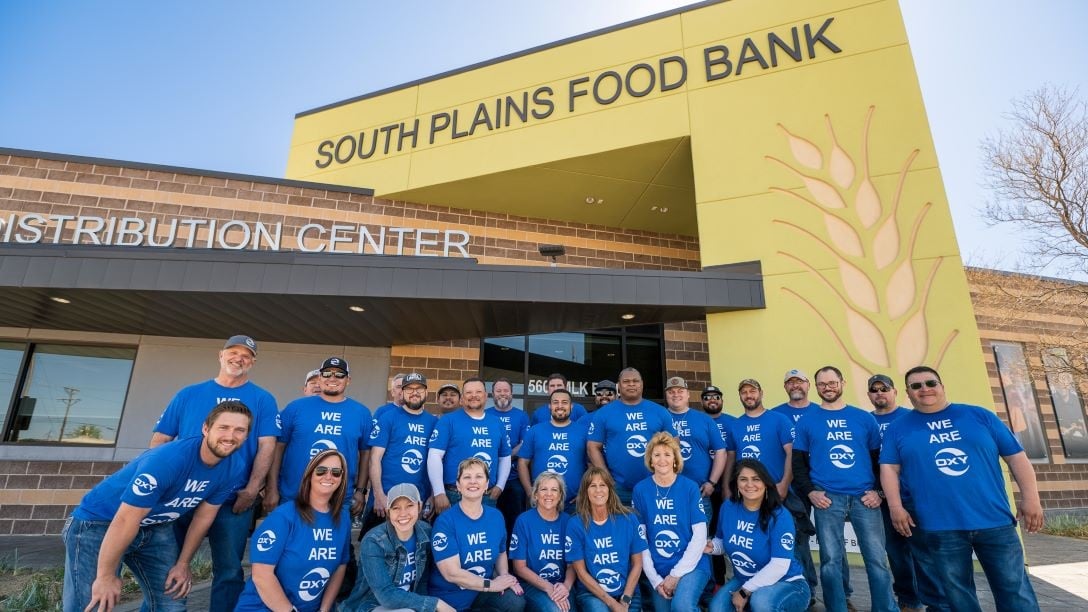
Prosperity
We seek to strengthen economies where we operate through local hiring, investments in our operations and infrastructure, and contributions to organizations that help communities develop and thrive. That includes taking time to listen to local leaders and neighbors, understand the regions where we operate, and engage in partnerships that address community needs and create economic opportunity and inclusive social development.
By investing our time and resources in programs and initiatives that support the areas surrounding our operations where our employees live and work, we seek to advance our relationships with neighboring communities and promote mutually beneficial outcomes.
Publications
Resources
- HSE & Sustainability Principles
- Sustainability Report
- 2023 Sustainability Performance Highlights and Progress
- Climate Report
- Annual ESG Data Summary
- Human Rights Policy Statement
- Climate Advocacy and Engagement
- Climate Policy Positions
- Oxy CDP Submission 2024
- 2023 Independent Assurance Statement
- 2022 Independent Assurance Statement
- 2019-2021 Independent Assurance Statement
Historical versions of our reports are located in the Publications Archive.