Doing Business With OxyChem
Reliably supporting your mission
For more than 100 years, OxyChem has built a reputation for innovation, reliability and responsibility in the supplying of essential chemicals. We count on best-in-class partners, advanced technologies, streamlined supply chain processes, proactive sustainability practices and the highest ethical standards to maintain excellence.
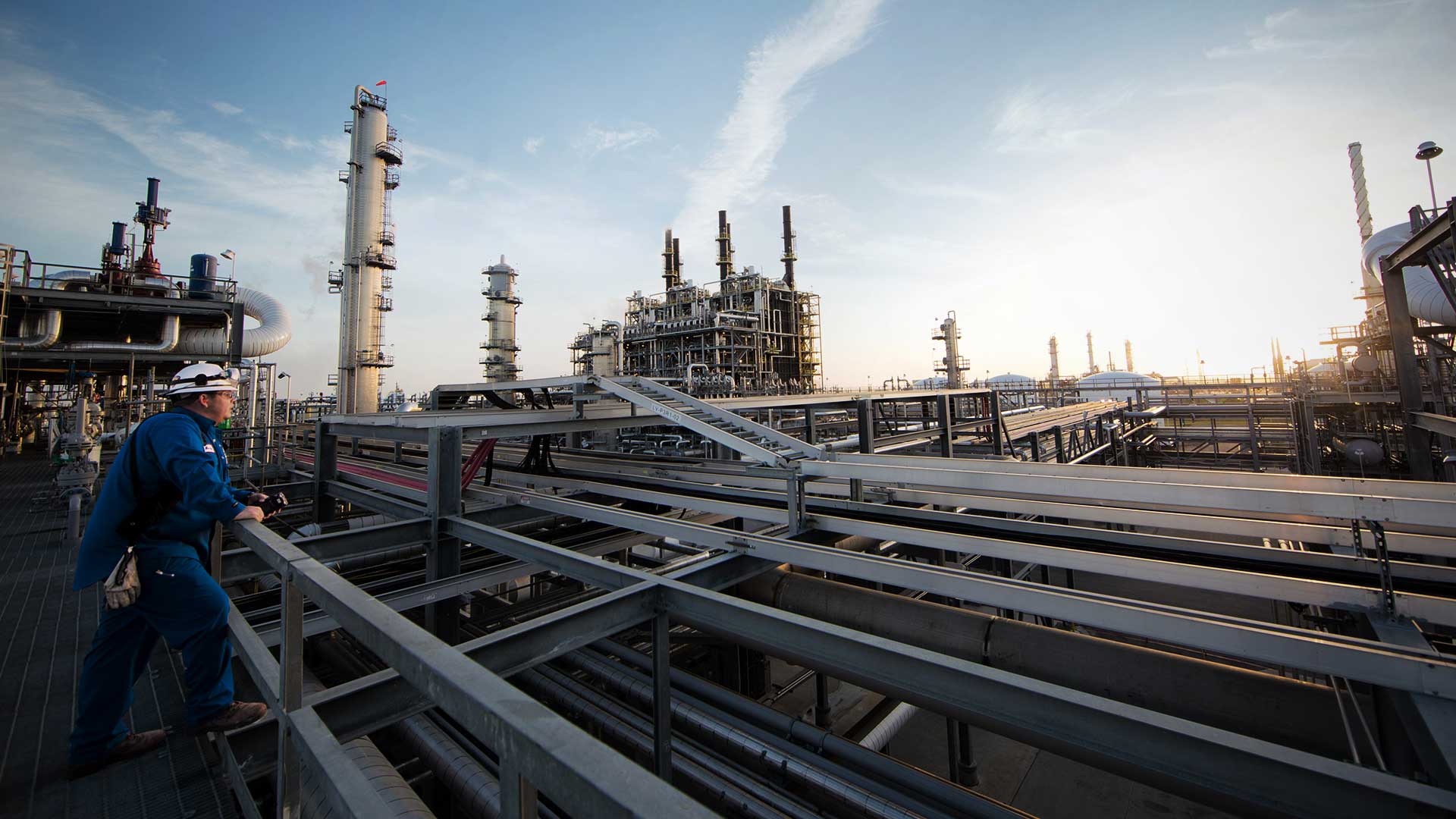
Doing Business with OxyChem
Customer and Technical Services
Customer and Technical Services
OxyChem has a reputation for being easy to work with—and it’s a reputation our representatives work hard to maintain. Our customer and technical services professionals collaborate with customers to help reduce supply chain costs wherever possible. All while providing informed, personalized service that gets the details right.
We understand the critical role a customer service rep can play in a chemical buyer’s order, operations and overall experience. That’s why we put only dedicated, knowledgeable professionals on each account and ensure that they truly understand your specific needs.
eCommerce Portal
Sales Tax Exemptions
Sales Tax Exemptions
OxyChem will remove sales tax from those customers that present a valid tax exemption certificate. To meet sales tax exemption requirements, please note the following qualifications below.
- A sales tax exemption certificate is required from the state that the product is being shipped to.
- Sales tax will be charged until we receive the appropriate state's exemption certificate.
- Ensure the Name and tax ID on your exemption certificate match those registered with the state and your OxyChem account.
Your exemption certificate will be verified and applied within one business day.
If you believe that the tax was charged in error or have questions about your OxyChem account name, please contact chemicals@oxy.com.
*Required Field
By clicking this link, you will be taken away from Oxy's website and to Vertex's Exemption Certificate Wizard. Please review Vertex's Terms and Conditions, Privacy Policy, and other documentation for more information on their services.
Vendor Managed Inventory
Vendor Managed Inventory
Our Vendor Managed Inventory (VMI) program monitors, tracks and automatically replenishes inventory for OxyChem customers. By integrating supply chain and enterprise data and establishing desired business rules, we can make sure you always have the essential chemicals you need.
Our VMI platform uses electronic railcar tracking and telemetry devices on storage vessels to provide real-time inventory information. The system re-orders once inventory hits threshold levels with no action required on the part of the buyer. Participants optimize inventory, avoid demurrage and alleviate expedited shipments.
Supply Chain Integration
Supply Chain Integration
OxyChem’s Business-to-Business (B2B) Supply Chain Integration service uses electronic document exchange to streamline the chemicals supply chain. This service digitizes production plans, purchase orders, sales orders, order confirmations, shipping notices, invoices and payments to virtually eliminate manual paperwork.
An industry pioneer in these systems, OxyChem’s integration system can accommodate multiple communication protocols and exchange standards, including XML, ebXML, EDI, CIDX and IDocs. That means less transactional administration and efficiencies that really add up. The system complies with the California Transparency in Supply Chains Act of 2010.
Supply Chain Performance Management
Supply Chain Performance Management
OxyChem's Supply Chain Performance Management process improves supply chain efficiency through performance monitoring. This entails reviewing data and metrics with customers to identify possible supply chain improvements. The cornerstone of this program is our Supply Chain Scorecard, a custom report on supply chain efficiency between our company and the customer.
Supply chain efficiency is analyzed using logistics, order and billing data. Logistics data will include shipment history, rail trip and transit times, rail inventory and demurrage, non-optimum shipments and returns. Order information will include on-time shipments, percent of orders automated and percent of VMI sales. Billing will include percent of automated invoices, number of debit and credit memos, percent of billing adjustment and on-time payments.
Customer and Technical Services
OxyChem has a reputation for being easy to work with—and it’s a reputation our representatives work hard to maintain. Our customer and technical services professionals collaborate with customers to help reduce supply chain costs wherever possible. All while providing informed, personalized service that gets the details right.
We understand the critical role a customer service rep can play in a chemical buyer’s order, operations and overall experience. That’s why we put only dedicated, knowledgeable professionals on each account and ensure that they truly understand your specific needs.
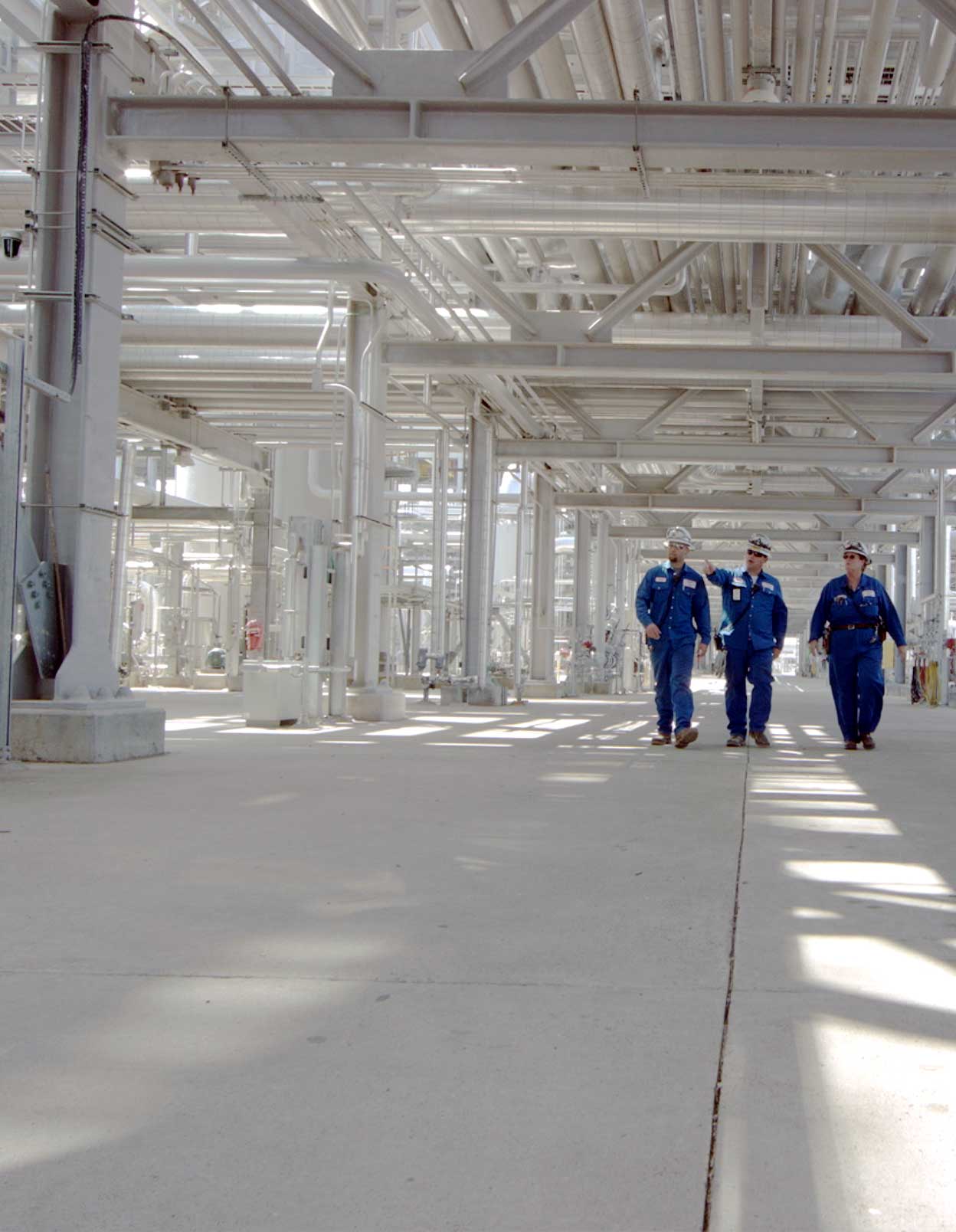
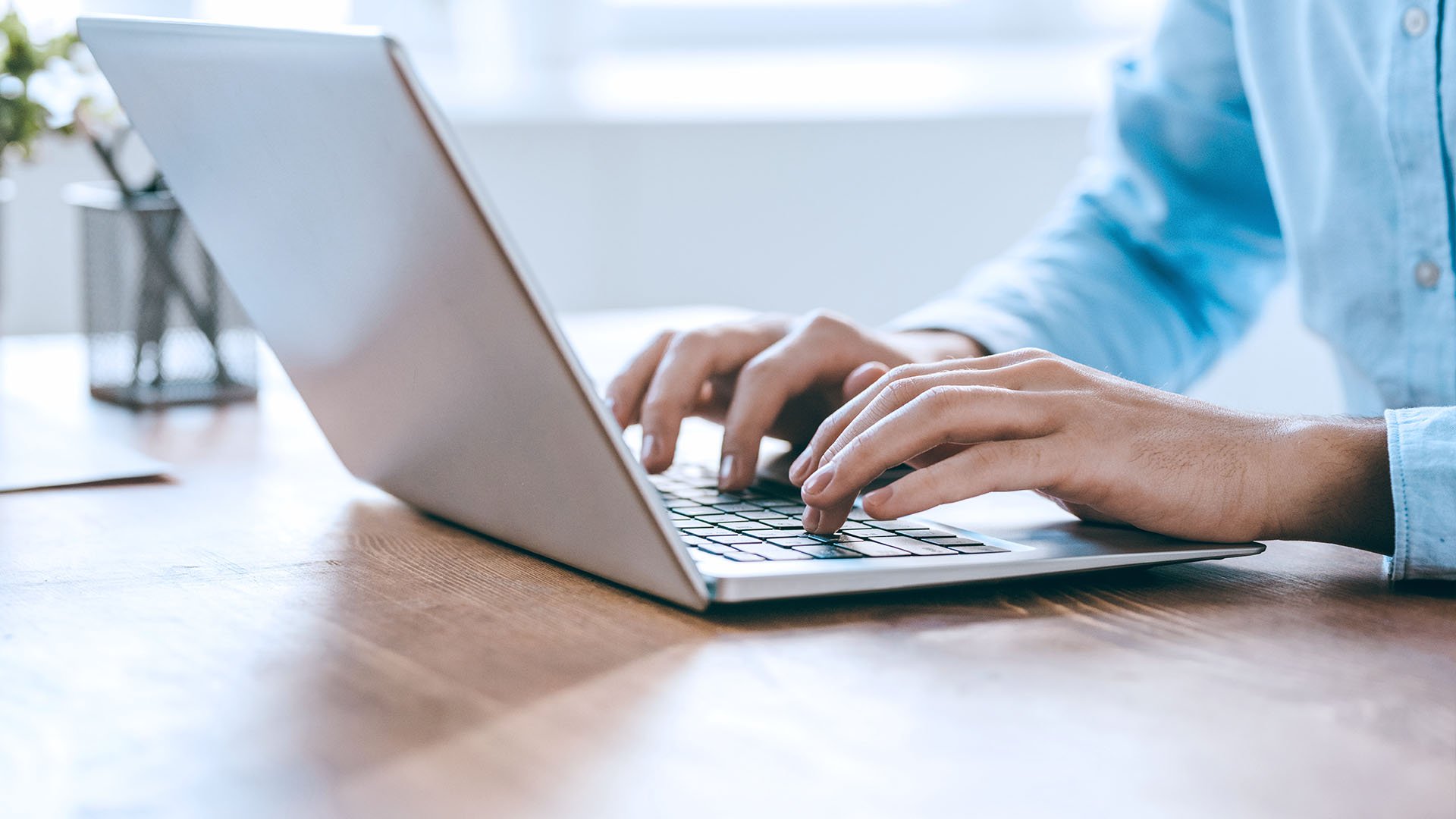
Sales Tax Exemptions
OxyChem will remove sales tax from those customers that present a valid tax exemption certificate. To meet sales tax exemption requirements, please note the following qualifications below.
- A sales tax exemption certificate is required from the state that the product is being shipped to.
- Sales tax will be charged until we receive the appropriate state's exemption certificate.
- Ensure the Name and tax ID on your exemption certificate match those registered with the state and your OxyChem account.
Your exemption certificate will be verified and applied within one business day.
If you believe that the tax was charged in error or have questions about your OxyChem account name, please contact chemicals@oxy.com.
*Required Field
By clicking this link, you will be taken away from Oxy's website and to Vertex's Exemption Certificate Wizard. Please review Vertex's Terms and Conditions, Privacy Policy, and other documentation for more information on their services.
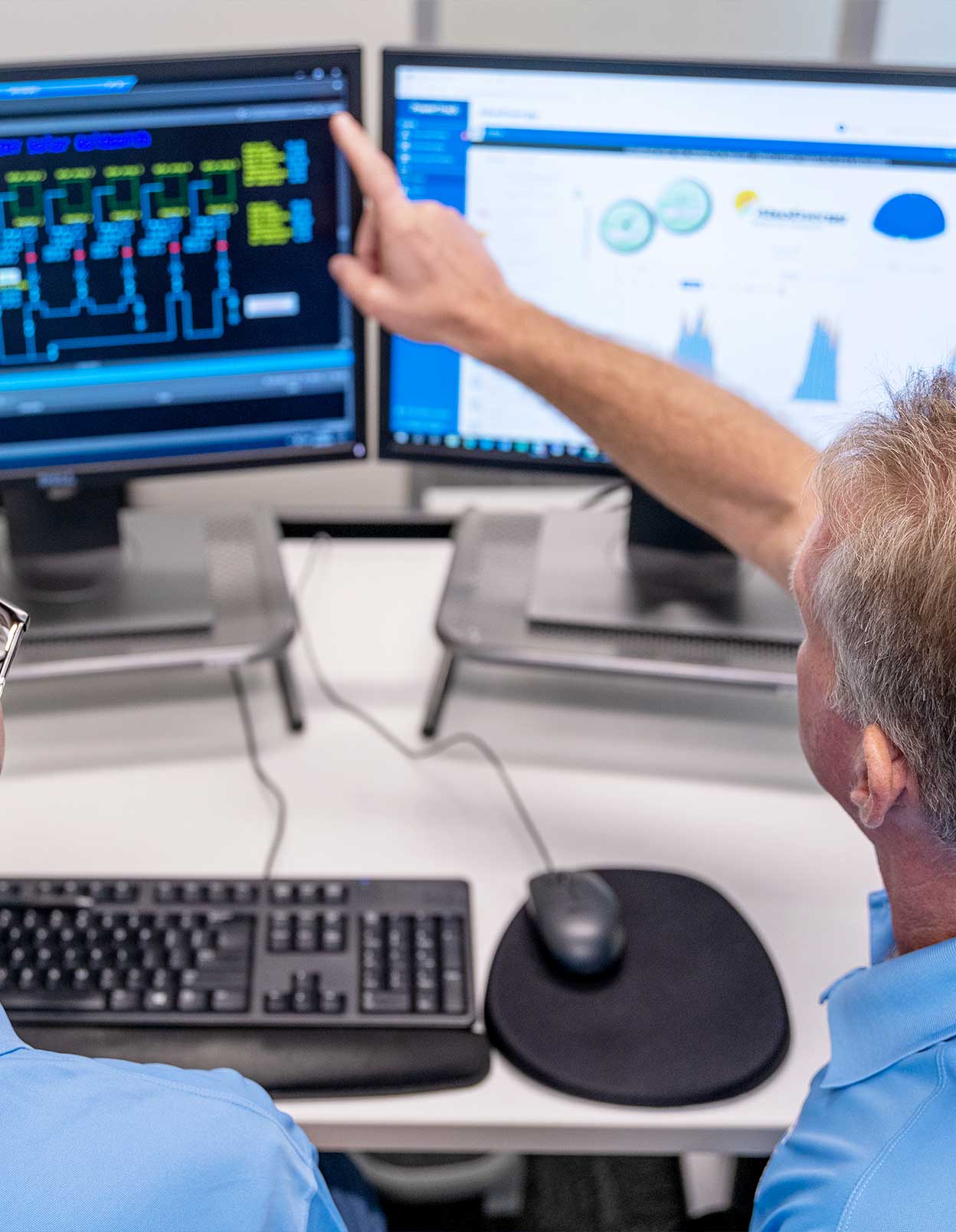
Vendor Managed Inventory
Our Vendor Managed Inventory (VMI) program monitors, tracks and automatically replenishes inventory for OxyChem customers. By integrating supply chain and enterprise data and establishing desired business rules, we can make sure you always have the essential chemicals you need.
Our VMI platform uses electronic railcar tracking and telemetry devices on storage vessels to provide real-time inventory information. The system re-orders once inventory hits threshold levels with no action required on the part of the buyer. Participants optimize inventory, avoid demurrage and alleviate expedited shipments.
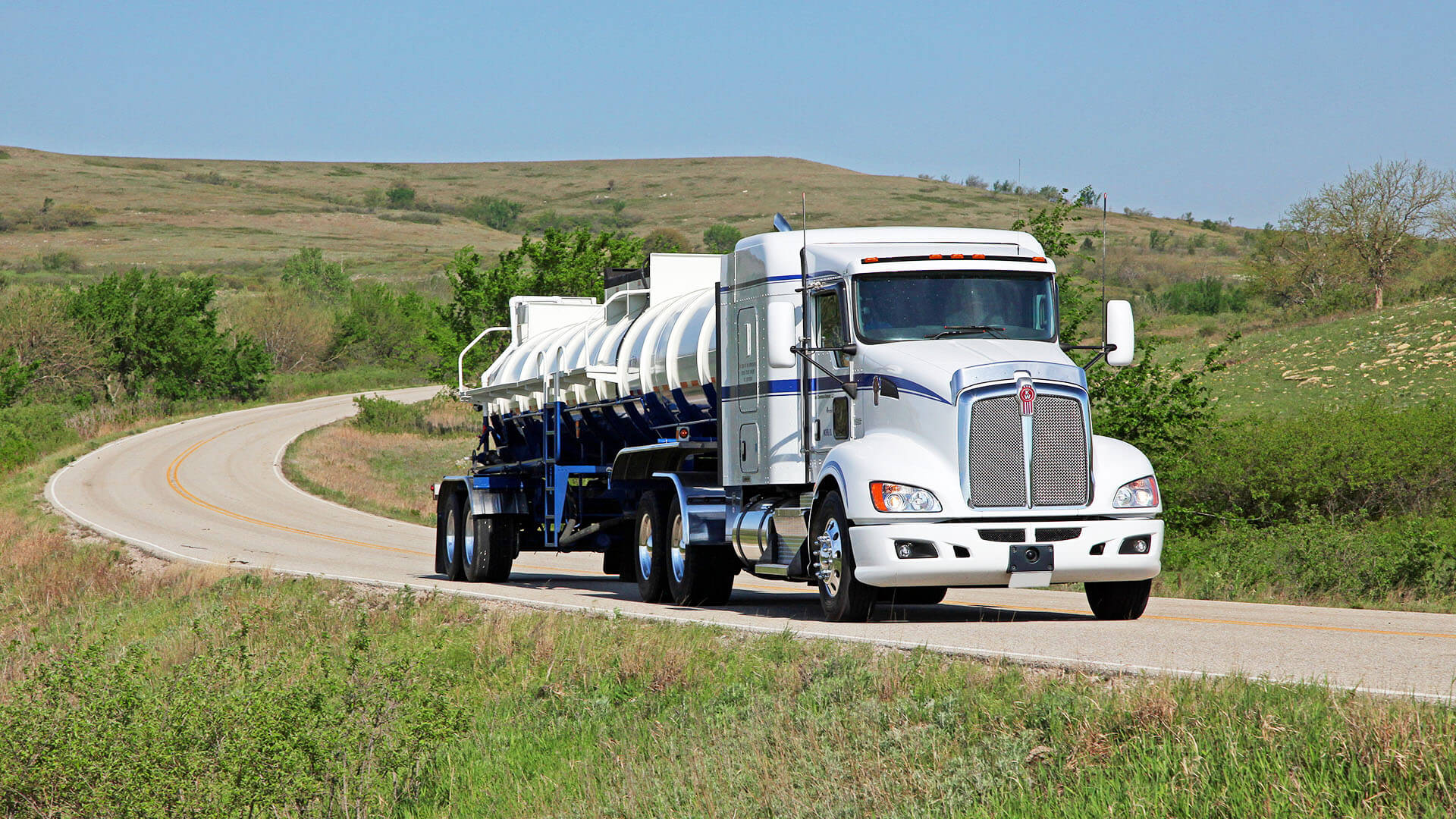
Supply Chain Integration
OxyChem’s Business-to-Business (B2B) Supply Chain Integration service uses electronic document exchange to streamline the chemicals supply chain. This service digitizes production plans, purchase orders, sales orders, order confirmations, shipping notices, invoices and payments to virtually eliminate manual paperwork.
An industry pioneer in these systems, OxyChem’s integration system can accommodate multiple communication protocols and exchange standards, including XML, ebXML, EDI, CIDX and IDocs. That means less transactional administration and efficiencies that really add up. The system complies with the California Transparency in Supply Chains Act of 2010.
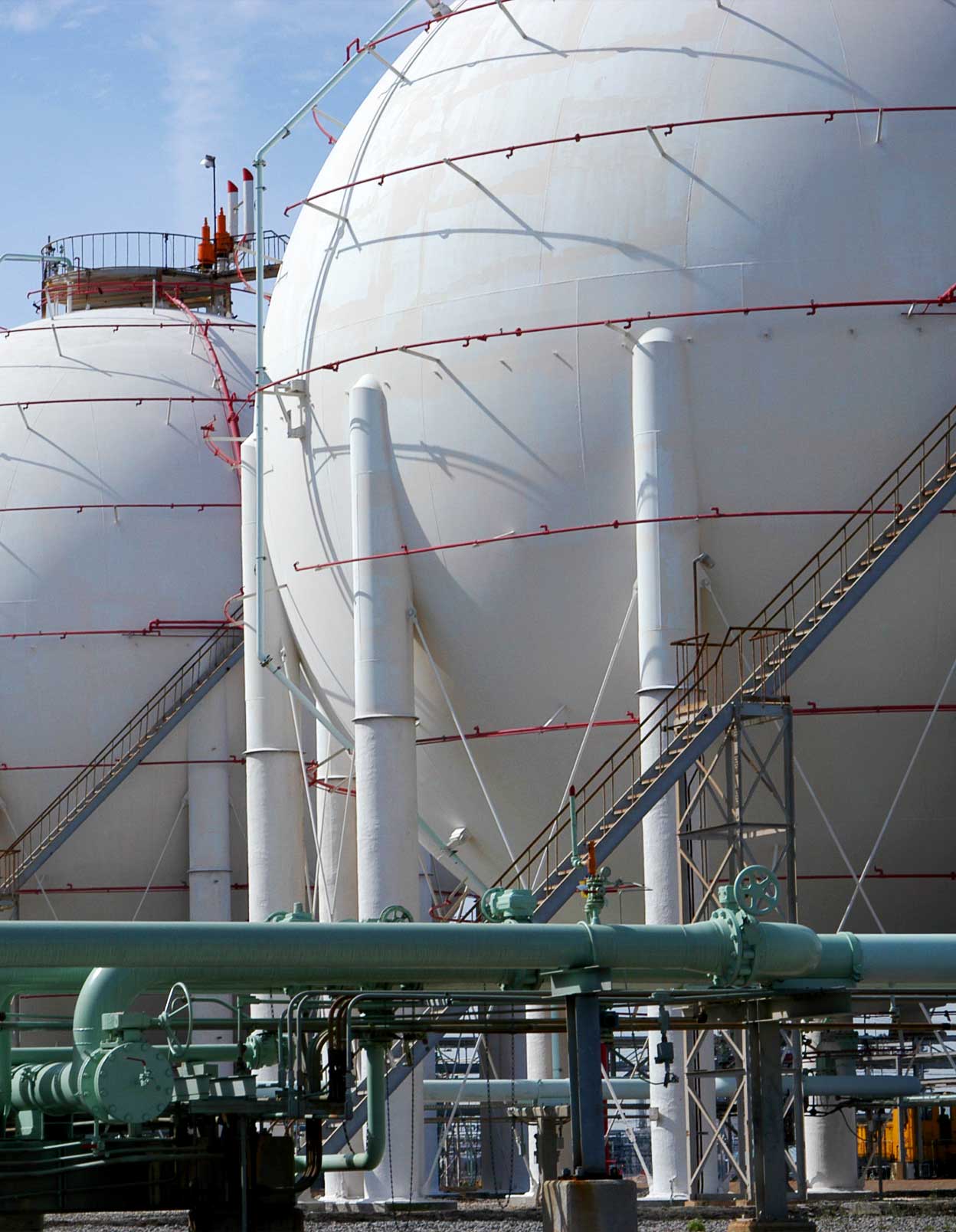
Supply Chain Performance Management
OxyChem's Supply Chain Performance Management process improves supply chain efficiency through performance monitoring. This entails reviewing data and metrics with customers to identify possible supply chain improvements. The cornerstone of this program is our Supply Chain Scorecard, a custom report on supply chain efficiency between our company and the customer.
Supply chain efficiency is analyzed using logistics, order and billing data. Logistics data will include shipment history, rail trip and transit times, rail inventory and demurrage, non-optimum shipments and returns. Order information will include on-time shipments, percent of orders automated and percent of VMI sales. Billing will include percent of automated invoices, number of debit and credit memos, percent of billing adjustment and on-time payments.
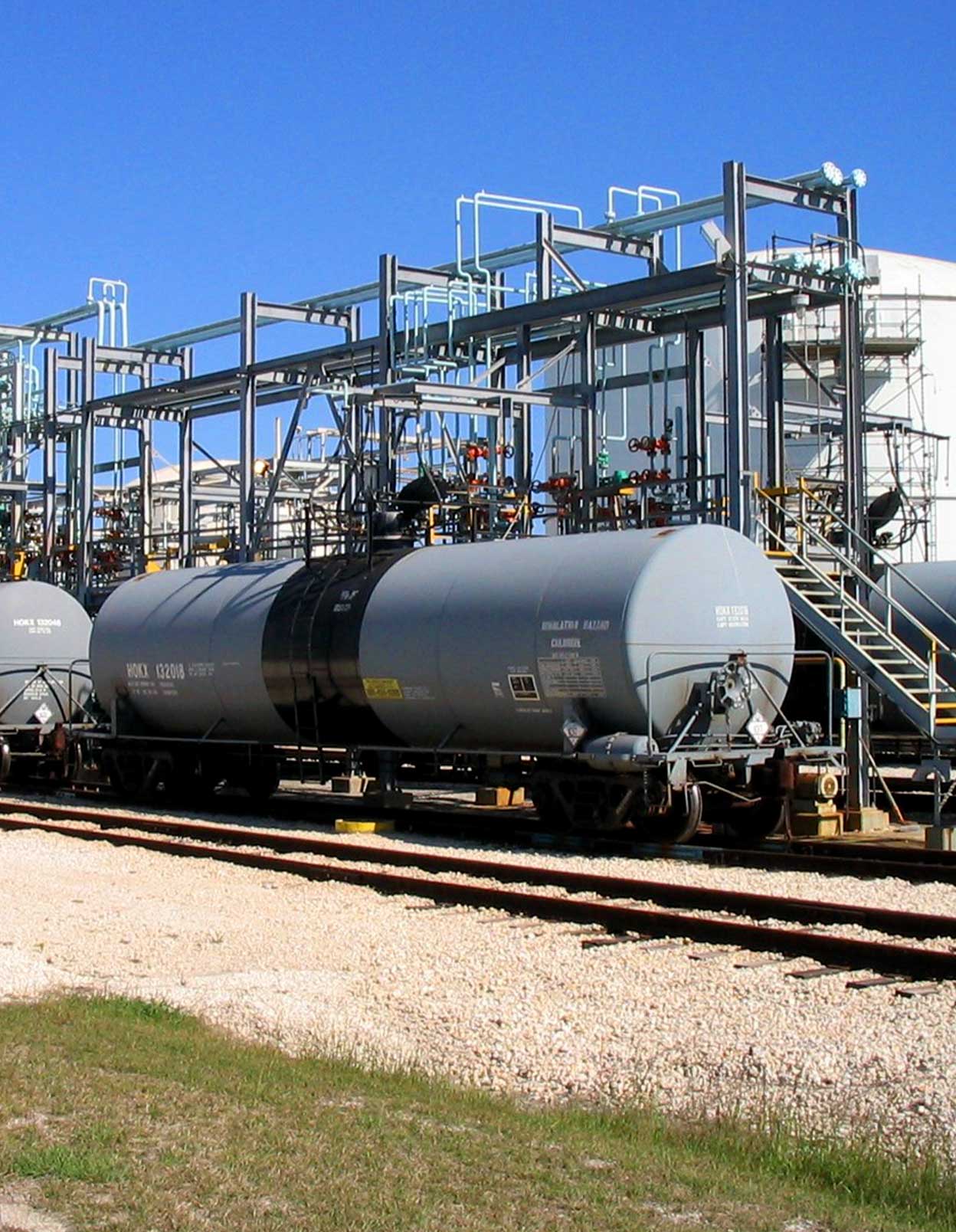
Technical Expertise and Licensing
Advancing the technology of chemical manufacturing
OxyChem’s deep technical expertise is reflected in its licensing to other manufacturers globally, along with our support for customers through our Technical Centers.
- OxyChem develops and licenses its EDC and VCM technologies to qualified manufacturers around the world.
- Our licensing program provides highly trained technical specialists with expertise in process design and development, training, start-up assistance and an effective, ongoing technical assistance and support program.
- Our EDC and VCM technology licensing program also includes a "know-how" exchange program that facilitates meetings every two years for participating licensees to discuss and exchange improvement ideas and technological advances.
- OxyChem’s Technical Centers are staffed with accomplished chemists and equipped with state-of-the-art technical equipment. This allows us to develop new products, advance manufacturing process improvements and provide highly accurate analyses supporting OxyChem customers and manufacturing locations.
Prospective Suppliers
Strong products and services. Great communication and collaboration. Dedication to continuous innovations in product quality and customer service. If your team is ready to Zero In on excellence, we want to hear from you.
Regional purchasing offices in Convent, Louisiana; Houston, Texas; and Niagara Falls, New York, handle purchase order transactions and procurement needs for all OxyChem facilities. National indirect and raw material contracts are managed at OxyChem's corporate office in Dallas, Texas.
New business awards are based on price, performance, quality and other requirements. New contractors undergo a pre-qualification process that includes review of the contractor’s annual safety performance and sustainability practices.
OxyChem operates under a strict Code of Business Conduct, and expects that its suppliers will abide by OxyChem’s Supplier Code of Conduct (PDF). The OxyChem Supplier Code of Conduct outlines the compliance standards we expect from contractors and suppliers working for OxyChem. This includes applicable internationally recognized environmental, social and corporate governance standards and the American Chemistry Council’s Responsible Care® program.
Meeting the highest standards of integrity, promoting human rights and protecting the health, safety and security of our workforce, neighboring communities and the environment are among OxyChem’s highest priorities. We strive to integrate these considerations in every aspect of OxyChem’s operations.
To learn more about becoming a supplier, or to find out if there is a current or expected requirement for your goods or services, please email OxyChem Purchasing. Please note that acknowledgement of an email does not imply a contract or intent to purchase goods or services from a prospective supplier by OxyChem.